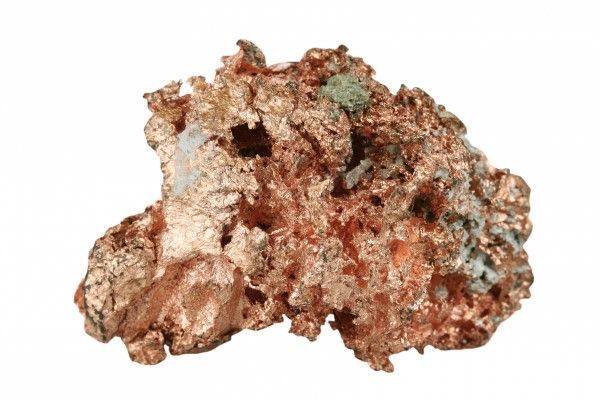
Согласно отчету, опубликованному Международной группой по изучению меди (ICSG), на мировом рынке рафинированной меди в 2023 году отмечался дефицит в размере 87 000 тонн по сравнению с дефицитом, равным 434 000 тонн, в 2022 году.
В 2023 году, по данным Геологической службы США (USGS), мировые запасы меди оценивались в 1 млрд тонн, с крупнейшими долями у Чили (190 млн тонн), Перу (120 млн тонн), Австралии (100 млн тонн), России (80 млн тонн), Мексики (53 млн тонн) и США (50 млн тонн).
Добыча медной руды в этом году достигла 22 млн тонн, ведущими производителями были Чили, Перу, Китай и США.
Всемирное бюро статистики металлов (WBMS) сообщает, что производство рафинированной меди составило 27,6261 млн тонн, а потребление — 27,6919 млн тонн, с дефицитом поставок в размере 65,800 тонн.
По данным Международной группы по изучению меди (ICSG), дефицит рафинированной меди в 2023 году составил 87,000 тонн, что меньше, чем 434,000 тонн в 2022 году.
В каком виде медь встречается в природе?
Источником меди служит медная руда, а также отходы этого металла и сплавов с ним. Процент содержания меди в руде может находиться в диапазоне 1–6%. Со временем руда с высоким содержанием цветных металлов, в том числе меди, стала встречаться всё реже. Например, в XIX веке её добывали из руды с содержанием от 6 до 9% этого металла, а в настоящее время руды, содержащие 5% меди — это редкость. В промышленном секторе многих стран источником меди служат руды, содержащие всего 0,5% данного элемента.
В руде этот цветной металл, как правило, встречается как сернистое соединение (например, Cu2S (халькозин ), CuFeS2 (медный колчедан), CuS (ковелин )) или оксид (CuO (тенорит ), Cu2O (куприт )), а также в виде гидрокарбонатов (CuCO3 × Cu(OH2) (малахит), 2CuCO3 × Cu(OH)2 (азурит )).
Как происходит процесс рафинирования?
Чтобы получить чистый цветной металл пригодный для изготовления медных листов, прутков, медных шин, из черновой меди нужно удалить примеси путём рафинирования. Этот процесс позволяет исключить лишние элементы, ухудшающие свойства металла (например, фтор, свинец и др.), а также выделить ценные элементы (например, золото, никель, галлий, серебро, и др.). В настоящее время черновую медь рафинируют электролитическим или пирометаллургическим способом, и часто это делают последовательно.
Пирометаллургический метод
Пирометаллургическое (или огневое) рафинирование проводится в отражательных печах, вмещающих до 0,4 килотонн руды.
Цикл очистки, как правило, продолжается от 12 до 16 часов и включает этапы:
- окисление примесей;
- исключение растворившихся газов («дразнение на плотность»);
- раскисление («дразнение на ковкость»);
- разливка меди и отливка анодов.
Когда эти операции выполняются на производстве, специализирующемся на выпуске черновой меди, она заливается в печь в жидком виде, а общая длительность цикла существенно уменьшается.
Примеси окисляются воздухом, вдуваемым посредством специальной стальной трубки ⌀ 20–40 мм, покрытой огнеупорными материалами.
Окислившиеся примеси поднимаются на поверхность расплавленной меди, в результате чего образуется шлак. Чем быстрее он удаляется, тем глубже происходит очистка. Некоторые летучие окислы при этом частично становятся парообразными. Подобным способом устраняется существенная часть алюминия, железа, никеля, кремния, цинка, серы, марганца, олова и свинца. Частично уходят примеси сурьмы, мышьяка, висмута. Такие элементы как золото, серебро, а также селен и теллур не окисляются и остаются в меди.
Дразнение на плотность — процесс удаления растворенных газов из меди. Это происходит путём погружения внутрь ванны сырой древесины — она разлагается, выделяя испаряющуюся воду, а также газообразные углероды. В результате металл бурно перемешивается — за счёт этого из него удаляются сернистые и прочие газы.
Очищенная медь выходит из печи через длинное вертикальное отверстие в её стенке. После пирометаллургической очистки металл поступает в машины для разливки, где отливаются аноды. Их масса может составлять от 250 до 320 кг. Если полученная медь имеет большое количество включений из благородных металлов (золото, серебро, платина), то полученные плиты в дальнейшем отправляются дополнительно на очистку электролитическим методом.
Электролитический метод
Этот вариант позволяет на выходе добиться практически чистого продукта. Для очистки используются аноды в виде пластинок размерами около 70–90 см в ширину и 70–100 см в длину. Толщина анодов обычно составляет от 3 до 5 см. В их конструкции также предусмотрены шины для подвода электротока или ушки для опоры о бортики ванны. В качестве катодов в ваннах используются тонкие катодные листы из чистой меди. Они соответствуют ГОСТ 546, их толщина может составлять от 4 до 6 мм.
Ванны для электролиза, как правило, имеют прямоугольную форму. В настоящее время их обычно изготавливают из железобетона. Внутренняя часть облицовывается материалами, устойчивыми к воздействию кислот (это может быть свинец, винипласт и др.). В качестве электролита используется водный раствор CuSO4 и H2SO4: 35-50 г/л сульфата меди и 125-230 г/л серной кислоты.
Катоды и аноды помещаются в электролитические ванны — их размещают параллельно, чередуя друг с другом. Расстояние между центральными частями одинаковых электродов должно составлять 9–12 см. В ванне обычно находятся 24–49 пар электродов, при этом анодов всегда на единицу меньше. Аноды и катоды подключаются к источнику постоянного тока. Причём первые — к полюсу с зарядом «+», а вторые — к полюсу с зарядом «-» соответственно. Ванны электролиза соединяются последовательно, объединяясь в блоки.
Когда медь начинают рафинировать, анод (черновая медь) постепенно уменьшается, растворяясь — при этом лишние примеси частично выпадают в виде осадка на дно, а часть из них растворяется в электролите. В это время «чистая» медь «оседает» на катоде, объём которого постепенно увеличивается.