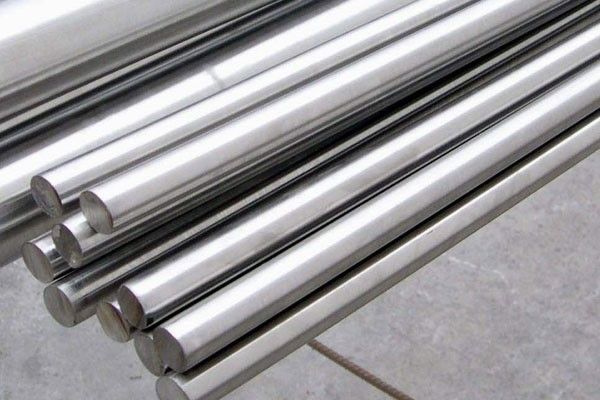
Сталь — это сплав железа с углеродом и другими элементами, который широко используется в промышленности благодаря своим уникальным механическим свойствам и доступности. Классификация сталей может быть выполнена по различным критериям, включая состав, метод производства, назначение, микроструктуру и термическую обработку. Разберем подробнее основные виды и классификацию сталей.
Классификация по химическому составу
Углеродистые стали
Это наиболее распространенный тип сталей, содержащих углерод в пределах от 0.02% до 2.14%. Углеродистые стали делятся на три подкатегории:
- Низкоуглеродистые (малоуглеродистые) стали (до 0.25% углерода) используются для изготовления кузовных деталей автомобилей, строительных профилей.
- Среднеуглеродистые стали (от 0.25% до 0.6% углерода) применяются для производства рессор, шестерен.
- Высокоуглеродистые стали (от 0.6% до 2.14% углерода) используют для изготовления режущего инструмента и рессор.
Легированные стали
Это тип стали, в состав которой включены специфические добавки других элементов помимо углерода, что придаёт ей улучшенные механические свойства и специализированные функции. Эти дополнительные элементы называются легирующими добавками, и они значительно изменяют характеристики сплава, такие как твёрдость, прочность, коррозионная стойкость, термоустойчивость и многие другие. Сюда относятся и нержавеющий металлопрокат.
Основные легирующие элементы и их влияние:
- Хром (Cr): Увеличивает устойчивость к коррозии и окислению, улучшает прочность на растяжение, твердость и износостойкость. Нержавеющая сталь, содержащая более 10.5% хрома, является примером использования этого элемента.
- Никель (Ni): Улучшает прочность, вязкость и коррозионную стойкость, особенно в агрессивных условиях и при низких температурах. Никель делает структуру стали аустенитной, что придает ей не магнитные свойства.
- Молибден (Mo): Повышает прочность и жаропрочность, улучшает устойчивость к коррозии и ускоряет закалку. Это особенно важно для сталей, используемых в нефтегазовой промышленности и энергетике.
- Ванадий (V): Увеличивает твердость и устойчивость к ударным нагрузкам. Также способствует улучшению зернограничной прочности и предотвращает рост зерен при высоких температурах.
- Кобальт (Co): Улучшает жаропрочность и устойчивость к окислению на высоких температурах. Часто используется в сверхсплавах для газотурбинных двигателей.
- Титан (Ti) и Ниобий (Nb): Оба элемента препятствуют росту зерен при высоких температурах, увеличивают прочность и устойчивость к межкристаллитной коррозии. Используются в сталях для сварных конструкций и в аэрокосмической промышленности.
- Марганец (Mn): Увеличивает прочность и устойчивость к износу, улучшает свариваемость и влияет на затвердевание стали при ее закалке.
Классификация по способу производства
- Кованые стали. Производятся методом ковки и обладают высокой прочностью и вязкостью.
- Литые стали. Используются для изготовления сложнопрофильных отливок, которые трудно или невозможно создать методами ковки или проката.
Классификация по назначению
- Конструкционные стали. Используются в строительстве и машиностроении для создания несущих конструкций и различных механических частей.
- Инструментальные стали. Применяются для производства инструментов, имеющих высокие требования к износостойкости и твердости.
Классификация по микроструктуре
Разделение на нижеописанные виды связано с внутренним строением стальных сплавов на микроскопическом уровне, которое определяется типом кристаллической решетки и распределением элементов в сплаве. Микроструктура стали в значительной степени влияет на её механические свойства, такие как твердость, прочность, ударная вязкость, коррозионная стойкость и термическая устойчивость.
Аустенитные стали
Эти стали имеют гранецентрированную кубическую решетку. Являются немагнитными и обладают хорошей коррозионной стойкостью и вязкостью при низких температурах. Наиболее известным примером является нержавеющая сталь типа 304 или 316, широко используемая в пищевой промышленности и для производства химического оборудования.
Ферритные стали
Имеют объемноцентрированную кубическую кристаллическую решетку. Они магнитны и обладают хорошей коррозионной стойкостью, но в сравнении с аустенитными сталями уступают в прочности и вязкости. Примеры включают некоторые нержавеющие стали, такие как AISI 430.
Мартенситные стали
Также характеризуются объемноцентрированной кубической кристаллической решеткой, но они формируются при быстром охлаждении (закалке) из аустенитного состояния. Мартенситные стали очень твердые и прочные, но при этом менее вязкие по сравнению с другими типами сталей. Они часто используются в производстве лезвий, медицинских инструментов и в условиях, требующих высокой износостойкости.
Бейнитные стали
Бейнит представляет собой структуру, которая формируется при промежуточной скорости охлаждения между быстрым охлаждением для мартенсита и медленным для перлита. Это делает бейнитные стали очень прочными и при этом сохраняющими хорошую вязкость. Используются в автомобильной промышленности и тяжелом машиностроении.
Перлитные стали
Перлит — это слоистая микроструктура, состоящая из чередующихся слоев феррита и цементита (карбида железа). Перлитные стали обладают умеренной прочностью и хорошей вязкостью. Они часто используются в строительных приложениях и для производства кованых деталей.
Классификация по термической обработке
- Закаленные и отпущенные стали. Эти стали обрабатываются для увеличения их прочности и усталостной долговечности.
- Нормализованные стали. Обработка позволяет улучшить механические свойства и структуру стали, делая ее более однородной.
Сертификация продукции изготавливаемой из стали
Продукция из стали, включая различные виды металлопроката как из черной, так и из легированной или нержавеющей стали, а также изделия из меди, алюминия и других металлов, подлежит строгой сертификации для подтверждения ее соответствия установленным стандартам и требованиям. Этот процесс важен не только для гарантии качества, но и для обеспечения безопасности и надежности конечных продуктов. В Казахстане и многих других странах СНГ основными нормативными документами, регламентирующими производство и использование стальных изделий, являются ГОСТы (государственные стандарты) и ТУ (технические условия).
Основные параметры сертификации металлопроката
- Сортамент. Этот параметр охватывает геометрические размеры изделий, такие как длина, ширина, толщина и допустимая кривизна. Точные спецификации сортамента гарантируют, что металлопрокат будет соответствовать техническим требованиям проектов и машиностроения.
- Химический состав стали. Качество и свойства стальных изделий в значительной степени зависят от их химического состава. Сертификация включает проверку содержания углерода, легирующих элементов и примесей, что напрямую влияет на коррозионную стойкость, прочность и температурные характеристики стали.
- Технические условия. Включают оценку механических свойств, таких как предел прочности, текучесть, удлинение при разрыве и ударная вязкость. Также рассматриваются условия отделки поверхности, что важно для предотвращения коррозии и улучшения внешнего вида изделий. Помимо этого, оценивается тип и структура стали, что может включать анализ микроструктуры и фазового состава.
Сертификат качества, оформляемый производителем, является документом, подтверждающим соответствие всех указанных выше параметров нормам и стандартам, что делает его неотъемлемой частью коммерческой деятельности и обеспечения доверия к продукции на рынке. При этом следует помнить, что процесс сертификации и стандарты постоянно эволюционируют в ответ на новые технологические достижения и изменения в промышленных требованиях. Такой подход гарантирует не только текущее, но и будущее соответствие продукции самым строгим критериям качества и безопасности.